Inline Blending: Efficient Continuous Mixing for Optimal Specifications
Inline blending is a controlled process that continuously mixes multiple components within a pipeline to achieve a defined specification. Unlike batch blending, inline blending offers numerous advantages, including reduced process time, flexibility for last-minute shipping schedule changes, improved accuracy, and reduced storage capacity and capital lockup.
Applications of Inline Blending
KPS inline blending solutions are versatile and can optimize profitability for various applications, including:
- Hydrogen
- Crude oils
- Fuel oils
- Bunker fuel
- Gas and condensate
- Ethanol products
Design Aspects of Inline Blenders
Key design considerations for inline blenders include:
- Existing infrastructure limitations
- Discharge performance
- Compatibility of different blend components
These constraints are typically identified and agreed upon during the project’s feed stage.
Performance Guarantee
Inline blending integrates the right components into a complete system. Proper material selection is crucial, depending on the liquid compositions. Valves, meters, and analyzers simultaneously measure and control blend components, ensuring adequate mixing and quality optimization at the blender header. KPS blending solutions are custom-designed, skid-mounted turnkey packages with an overall performance guarantee.
The selection of the proper blender control philosophy is dependent upon the constraints of the existing infrastructure, the quality of feedstock, and the final product specifications. The control system defines the stability and performance of the blender, and often requires a quality trim function that utilizes online analyzers to continuously optimize the performance of the blender. By using a combination of measured parameters (such as viscosity, density, sulfur and octane) and/or calculated flow-weighted quality parameters, quality trim blenders can automatically correct for any variations in the feedstock quality or errors arising from the blending models.
The blender philosophy can be migrated directly into the plant wide DCS control system to allow for a completely integrated solution for the plant that is fully supported by operation’s house contractor. Functionalities like recipe management, alarms, reports and batch information can be used up to its full potential and can customize their user interface to meet the requirement.
Blender Control Philosophy
The control philosophy depends on infrastructure constraints, feedstock quality, and final product specifications. The control system ensures blender stability and performance, often requiring a quality trim function that uses online analyzers for continuous optimization. By combining measured parameters (viscosity, density, sulfur, octane) and calculated flow-weighted quality parameters, quality trim blenders can automatically correct feedstock quality variations or blending model errors.
The control philosophy can be integrated into the plant-wide DCS control system, providing a fully supported, integrated solution. Features like recipe management, alarms, reports, and batch information can be fully utilized and customized to meet specific requirements.
Mixing Technology
For successful blending operations, stability, homogeneity, and consistency of the final product blend are crucial. Traditional static mixing devices create turbulence through baffles or metal plates, causing pressure loss and reduced throughput. These mixers are less attractive due to unstable results at the batch start and end.
The patented e-Jetmix™ technology offers an ideal solution with minimal pressure drop and stable performance regardless of flow rate. The e-Jetmixer™ ensures long-term stable blending and homogeneous flow, essential for real-time blender optimization and minimized give-away. The efficient KPS e-Jetmixer™ design includes an external pump, mixing nozzle, and take-off point. A portion of the main stream is extracted and re-injected using the patented KPS nozzle, with online analyzers and CS-01 cell samplers located in the loop for accurate measurements.
CFD Simulation for Blender Design
KPS uses advanced CFD simulation software to verify installation designs, addressing complex variations in densities, viscosities, and flow rates. This tool ensures accurate and stable blending results across the entire operating envelope, eliminating reliance on rule of thumb or previous experiences.
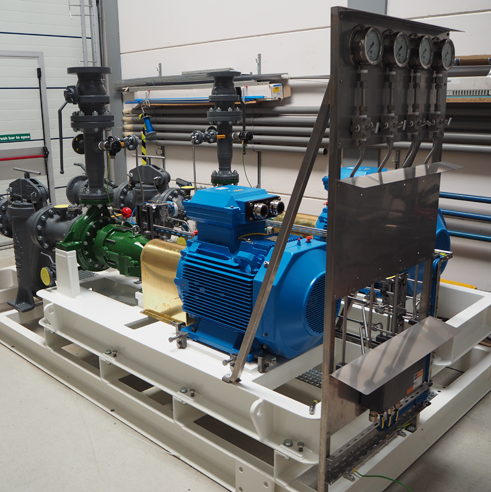
Get in contact with our experts!
Send your e-mail and we’ll get in touch!